Single-mode lasers delivered via an intelligent "oscillating" head allow precise control of weld dimensions and heat input for welding medical devices.
While many existing medical device production lines use Nd:YAG pulsed lasers, most new lines use QCW multi-mode fiber lasers, which have similar beam and pulse characteristics to the Nd:YAG laser while offering the low operating cost benefits of fiber lasers.
When developing medical devices and medical instruments, one basic rule usually applies - a new product is always smaller and more complicated than its predecessor. As a consequence, weld size requirements and welding precision and accuracy are ever increasing. And along with this, the requirements for heat input control are also increasing. The problem is that pulsed lasers, which are often used for welding, can sometimes be limiting in terms of material selection because the high weld cooling rates can create a tendency for weld cracking. Is there another welding option?
Why single-mode fibre lasers are the solution
A single-mode continuous-wave fiber laser (CW laser) in conjunction with a scanning head offers a unique and compelling welding option: weld miniaturization - precise control of weld dimensions and heat input.
For those not as familiar with single-mode lasers, single-mode lasers have the absolute best beam quality and, as a result, generate the smallest spot size for a given focal length of optics. In fact, single mode lasers typically focus to a focal diameter in the range of 25 µm (0.0025 mm) using a focal length of 150 mm (6").
The advantage is that by coupling a single-mode laser source to a scanning workhead, we gain the ability to move a 25 µm spot fast enough across the workpiece to scale the heat source as needed. Thus, if a 100 µm wide weld is required, the 25 µm point will move rapidly perpendicular to the direction of the seam, creating the required weld width of 100 µm. However, the movement of this point will be fast enough that the material will react the same in terms of heat input as if a larger diameter point were used.
The rapid movement on the part produced by the scanning head is made possible by two very small, low inertia mirrors, called galvanometers or 'heads', which are mounted perpendicular to each other and are therefore capable of producing movement in the X and Y axes. The F-Theta lens then produces a flat focal plane, so that over a 100x100mm or 200x200mm area (depending on the focal length of the optics) the laser remains focused over the entire area.
The laser point can thus move anywhere in the entire working area and create any shape or size of weld. In microwelding, this capability is a significant facilitator of the process.
Advantages of using single-mode fiber lasers:
1. It allows you to create any shape or size spot weld - it can be a circle, a ring, a spiral, a square, a smiley face, or anything that can be optimized for the thermal constraints of the part and the mechanical needs of the weld.
2. Dynamic weld scaling - different welds on the same part can be sized and shaped individually using only the toolpath instead of parameter changes, or welds on different parts can be scaled or shaped as needed.
3. Reduce cycle time for multi-point welds - even with linear actuators, moving between point welds is relatively slow compared to a scanning head that can move from one point to another in fractions of a second. A classic example of the use of scan heads for spot welding is the flexible arms that were once used for all disk drives, typically 25 spot welds are made in less than 1 sec.
4. Customizing weld dimensions - the lateral movement can be superimposed along the weld to precisely control the width and depth of the weld. For example, pulsed QCW or Nd:YAG reduces the cross-sectional depth of the weld from the centerline to the edge. With a single-mode laser and scanning head, we can create a square cross-section profile so that the penetration at the center and edge of the weld is the same. Therefore, for butt or fillet welds, any seam misalignment can be accounted for without compromising the strength of the weld.
- On the left, a conventional cross-section and a cross-section of a spot created by the pulsed laser, spot size ~ 800 µm.
- On the right, cross-section and cross-section of a spot applied with a single mode laser, spot size ~ 30 µm, moving rapidly through the material.
5. Minimizing heat input - heat input is directly proportional to the strength of the heat source and the time applied to the part. The side effect of the heat source is a function of its size. By using a 25 µm point that moves quickly across the part in any desired direction, we now have precise control over the heat input and all the control tools for optimization.
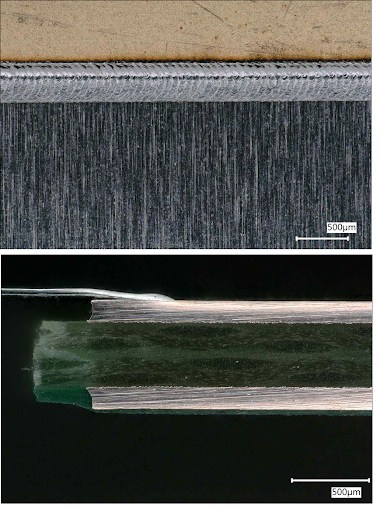
- Marketsegment.
- Material: Stainless steel foil, 40 µm, to gold-plated copper, 140 µm.
- Application.
- Laserused: PowerLine FL 150 P
- Working head: SmartWeld+
- Linear speed: 800 mm/min
- Weldingdepth: ~ 45 µm
- Shear strength: 130 N per 10 mm
- Rating: Homogeneous seam, no cracks
- No visible impact on the circuit board
6. Large process windows, more weldable materials - with minimal heat input and a laser that operates in continuous mode, the cooling rate of the part is reduced, increasing the range of weldable materials while reducing the likelihood of weld cracks.
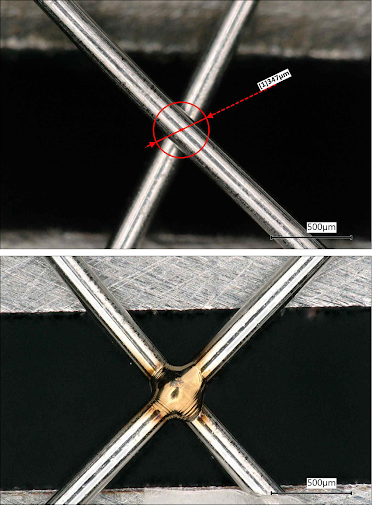
- Material.
- Application.
- Laserused: PowerLine FL 150 P, SmartWeld+
- Wire diameter: 200 µm
- Pointsize: 30 µm
- Number of pulses: One pulse
- Power: 85 W
7. 3D motion capability - the laser scanning head can be equipped with additional axes of motion to move the focal plane in the Z-axis, offering even more possibilities.
Advantages of single-mode fiber lasers
1. Lower laser power - using a focal spot size of around 25 µm increases the power density, which means that lower average power is required, reducing the required laser power and lowering acquisition and operating costs.
2. Lower acquisition costs - scan heads are a common commodity for laser marking due to their production volumes, so a high-tech scan head is relatively inexpensive even compared to fixed work heads.
3. Easy programming - programming the scan head movement does not require knowledge of G or M code, as the welding paths are created using circle and line functions just like in a drawing program, i.e. just like in marking lasers. The software guides the user through the preparation of the laser working path and the entire workflow, which may include the application of machine vision before welding, monitoring during the welding process or post-weld inspection.
4. Minimized system footprint - Typically, the laser working head has a working area of 200x200 mm (8x8") and is no larger than a small shoebox. The laser beam is fed into it by a fiber optic from the laser source, which is usually housed in a separate rack along with the control PC. The total area of the laser system is thus very small.
More than a laser scanning head
Although the acceleration and deceleration of the laser scan head are very high, they are still present, which means that some welding paths may have sections with higher or lower heat input.
Our Coherent SmartWeld+ intelligent "oscillating" head addresses this and adjusts the power and therefore the heat input on the fly. This fully flexible and programmable oscillation/power scheme allows precise control of weld heating and cooling - delivering more precise control of weld parameters, including weld width and penetration depth.
Read all about Coherent SmartWeld+technology and Coherent PowerLine FL laser sources .
Source.