Introduction - historical development of laser welding
The first laboratory experiments of laser welding appeared soon after the first laser prototypes were built in the early 1960s. However, the applications of laser welding became more prominent after the invention of the Nd:YAG laser in 1964 and with the gradual increase in the power achieved by CO2 lasers, initially in laboratories and towards the end of the 1960s in industrial deployment. At that time and in the following decades, CO2 lasers were also used for welding, mainly because of the higher absolute powers achieved. The disadvantage of CO2 lasers for welding applications is that the absorption of most structural materials is relatively low in the wavelength region of the CO2 laser (10.6 µm) compared to solid-state lasers with a wavelength of about 1.06 µm). See the graphs of material absorption versus wavelength presented in the previous part of the series. In addition, the efficiency of CO2 lasers is inherently an order of magnitude lower than that of e.g. fibre lasers . A major advantage of solid-state lasers is also the possibility of guiding the beam via an optical fibre to the weld site, compared to the complicated mirror assemblies in the case of CO2 laser beam guidance.
Advantages of laser welding
With the development and increasing performance of solid-state lasers (especially fibre lasers), laser welding has seen quite a meteoric rise in the last decade. Partly due to the development of more powerful and new types of lasers, partly also due to the wider use of new modern materials that are difficult to weld by other methods. This development has been due in no small part to the increasing demands for increased productivity and repeatability of the technological process. The main advantages of laser welding are weld quality, higher penetration depth, significantly lower Heat Affected Zone (HAZ), high productivity, easier automation, and last but not least, surface appearance and welding without additional material.
Other welding methods
This does not mean that other (conventional) welding methods do not have a permanent place in industrial applications. For example, electron beam welding in the aerospace industry - the weld quality is generally better despite higher acquisition and operating costs and a significantly lower welding speed. In contrast, TIG, MIG welding is fully sufficient for most common engineering applications and the acquisition and operating costs are significantly lower. The application itself, the automation and positioning requirements, the weld design and last but not least the economic context predetermine the use of suitable welding technology.
In addition to welding metallic materials and alloys, the laser is also successfully used for welding non-metallic materials, especially various plastics. However, this issue will be discussed in a special part of our series.
The principle of laser welding
The figure below shows schematically the two basic principles/mechanisms of laser welding.
In heat conduction welding (left part of the figure), the material is melted by absorption and conduction of heat by the incident laser beam. This process allows welding only to relatively small penetration depths. However, the welding speed can be higher and for some applications the comparison of the penetration depth and welding speed is satisfactory. Especially in those cases where welding speed is more important than narrow and deep penetration.
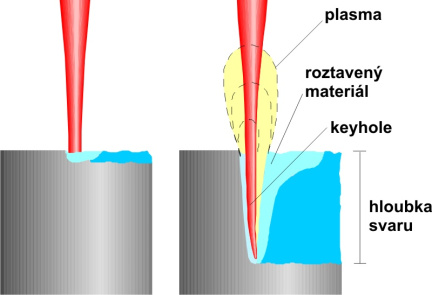
By increasing the areal power density, a critical value (empirically: 1-5 x 106 W/cm2) is reached where metal vapour formation occurs above the actual surface of the material being welded. Together with the high surface energy of the focused laser beam, plasma is generated and deep welding begins to occur. The laser beam forms a capillary that is 1.5 to 2 times the diameter of the focal point of the laser beam. The pressure of the gases exiting the capillary then prevents its closure. The plasma above the surface of the material then reverses the shape of the capillary. From the walls of the capillary, the embedded energy of the laser beam is then conducted into the melt and then into the solid material. This process allows the laser beam to penetrate deep into the material and creates a keyhole. This also significantly improves the absorption at the point of impact of the laser beam due to the multiple reflection inside the capillary. This creates a relatively narrow and deep weld. This is then the main reason why the laser beam is narrower than the predicted and theoretical path of the laser beam beyond its own point of focus. When the welding material itself or the focused laser beam moves, a weld seam is formed.
The actual welding process and its stability depend on many input parameters:
- the properties and parameters of the material to be welded
- the power/ or areal power density or pulse energy
- laser wavelength
- welding speed (feed rate)
- volume and type of assist gas
- polarization of the laser radiation and many other factors
- the parameters of the optical elements used in the welding head (not only the focal length) also play a significant role
- the position of the focal point of the focused beam relative to the nozzle and the surface of the material to be welded
The energy input of the laser beam is favourably influenced by the shielding (assisting) gas during laser welding. Commonly used assist gases (Ar, N2, CO2 or He) increase and stabilize the degree of absorption of the laser-induced plasma. Thus, the energy of the laser beam can almost completely penetrate the material after plasma formation and thus increase the keyhole effect. In addition, at the same time the assist gas is used to protect the cooling melt from oxidation. However, some materials can be welded without a protective atmosphere if the plasma formation allows it and the surface oxidation is acceptable.
Weldability of materials
In view of the above, the combination of the materials to be welded also plays an essential role. The table below gives basic empirical and indicative values. This is then essentially also true for the alloys of these basic materials. The table does not then go into more detail about the other circumstances of the requirements for the welds themselves, i.e. in terms of weld strength, hermeticity, appearance, etc.
Al | Ag | Au | Cu | Pd | Ni | Pt | Fe | Be | Ti | Cr | Mo | Te | W | |
---|---|---|---|---|---|---|---|---|---|---|---|---|---|---|
Al | V | |||||||||||||
Ag | U | U | ||||||||||||
Au | U | V | V | |||||||||||
Cu | U | U | V | V | ||||||||||
Pd | V | V | V | |||||||||||
None | U | V | V | V | V | |||||||||
Pt | U | V | V | V | V | V | ||||||||
Fe | U | U | D | D | D | V | ||||||||
In | U | U | U | U | U | |||||||||
Ti | U | U | U | U | U | U | U | U | V | |||||
Cr | U | D | D | V | V | D | ||||||||
Mo | U | V | D | V | V | |||||||||
Here | D | D | U | U | V | V | ||||||||
W | U | U | D | U | U | V | V | V | V |
V - very good, D - good, U - satisfactory
What type of laser to weld with (and what power)?
In the case of metallic materials, definitely a solid-state or diode laser with a wavelength in the near-infrared region (approx. 800 - 1070 nm). One of the basic arguments is clearly the small HAZ. And possibly also the high efficiency of solid-state lasers. Especially fibre lasers.
Far more important than the actual laser power (for continuous lasers) or the energy in the pulse (for pulsed lasers) is the so-called areal power density or areal energy density. That is, how small a point we can concentrate the power or energy of the respective laser source. In addition to the many other parameters that go into the laser welding process, listed in the preceding paragraphs.
As it is clear from the previous paragraph solid state lasers (Nd:YAG, disk, fiber) can be divided by their nature into pulsed and continuous lasers. Each has its unique representation in industrial applications. This topic has been discussed in more detail in previous parts of this series.
Nd:YAG lasers - pulsed and continuous wave (CW)
The output beam can be fed from the laser source to multiple output optical fibers, which can be switched between, and/or the output power of the laser source itself can be divided in a defined ratio to the individual optical fibers. Lamp-excited pulsed Nd:YAG lasers still have an indispensable place in many industrial laser welding applications, mainly due to pulse energies up to 70 Joules.
Currently, continuous Nd:YAG lasers are no longer manufactured by any major laser company and have been replaced by fiber lasers in all applications. Except for the so-called disk lasers, described in the next paragraph.
Disc lasers
These are essentially a modification of the Nd:YAG laser with a unique design of the laser resonator itself and the replacement of the active medium in the form of a rod with a thin disk of much smaller dimensions and with a more advantageous pumping principle using an array of laser diodes.
As a consequence, the quality of the output laser beam has been significantly improved compared to continuous Nd:YAG lasers. The laser principle itself is certainly unique and deserved some recognition at the time of its development, but the principle is quite demanding in terms of mechanical manufacturing and the efficiency itself is not significantly higher compared to Nd:YAG lasers. Currently, only one company offers this type of laser. This is probably due to the fact that it has fallen behind in the development of fibre lasers. It is only a matter of time before these types of lasers disappear from the offer of the unnamed company and are replaced by fiber lasers.
Diode lasers
Over the last few years, diode lasers, or arrays of laser diodes, have been used for some applications. This is either with direct beam guidance into focusing optics or with the option of being coupled into a fiber optic. The area in which the beam can be focused is larger compared to conventional lasers and therefore these lasers are mainly used for welding, coating and surface hardening. Due to the lower wavelengths (808nm, 940nm) these lasers can also be successfully used for welding some plastics. Another major advantage is the high efficiency and low weight/small size, i.e. suitable for combination with robotic workstations.
Fiber lasers
In the last 10 years or so, there has been quite an interesting discussion in the field of laser industrial technology, and subsequently its reflection in the number of laser systems installed with different laser sources: Fiber lasers versus CO2, Nd:YAG lasers and disk lasers. It is clear that pulsed Nd:YAG lasers still have their indispensable place in industrial welding applications. It is no coincidence that continuous Nd:YAG kilowatt lasers have disappeared from the offerings of all the leading laser companies. Similarly, welding applications with CO2 lasers are declining.
This is a unique type of laser in which radiation generation takes place inside a rare earth doped optical fiber. Similar generators have a number of advantages compared to conventional systems:
- excellent beam quality
- compactness
- low power consumption
- in principle, no additional optics are needed to bind the output to the fibre
Proven and fully functional systems with outputs up to 50kW are already widely available today. At the same time its size is comparable to a chilled beverage machine. Their massive deployment is no longer hindered by higher acquisition costs compared to other types of lasers.
Conclusion
It is indisputable that laser welding has become firmly established in developed industrial countries and it is gratifying that it is finding its own way in the Czech Republic not only to technologists but also to designers. It is nothing new nowadays when laser welding is directly prescribed on a product drawing. In many cases, it is necessary to design the appropriate weld with the use of lasers in mind during the actual product design.
In the next part of Laser Welding II of our series, some special aspects of laser welding will be discussed and then mainly some specific applications and also some practical experiences with regard to specific situations will be given.