Introduction - historical development of laser cutting
Laser cutting is the most widely used laser technology. The industrial use of lasers dates back to 1965 when the Western Electric Company built a working laser system for drilling diamond stamps. Then in 1967, a laser system for cutting steel plates using oxygen as an assist gas was commissioned in the UK. Systems for cutting non-metallic materials soon followed.
The 1970s then saw a more massive industrial deployment of laser cutting using CO 2 lasers. These systems were then further improved not only with regard to the development of the laser sources themselves. But significant improvements were also made to drives, control systems, post-processors, etc. However, laser sources have also made significant progress. One of the breakthroughs in the development of CO 2 lasers was the introduction of the so-called DC (Diffusion Cooled ) slab laser (see figuresbelow). This type of laser does not need external laser gas sources and there are no moving parts in the system. For this reason, these lasers have significantly lower operating costs compared to non-flow lasers and also a higher quality output beam. They are currently manufactured up to a power of 8 kW.
Towards the end of the last century, CO 2 lasers reached such high power levels that linear motors became more popular in the design of laser cutting machines, especially with the possibility of significantly higher cutting speeds. The use of solid-state lasers was also increasing, especially for thin sheet metal cutting.
The figure below shows absorption graphs of frequently cut materials. From these graphs it can be seen that the absorption in the wavelength region of solid state lasers (around 1 µm) is significantly higher than the absorption in the wavelength region of CO 2 lasers (10.6 µm).
The last ten years have been marked by the increased use of fibre lasers. Even renowned laser companies are now increasingly incorporating fibre lasers into their programme. The advantages of fiber lasers and a general overview of industrial lasers were discussed in more detail in the previous part of this series.
Types of laser cutting
3D laser cutting
It is through the use of fiber lasers that spatial cutting becomes much easier. The laser cutting head is placed on the flange of the last axis of the robot. The laser beam is fed to the cutting point by an optical fiber, which makes the integration of the laser onto the robot very simple. In the case of cutting precise holes in 3D, the cutting head can be placed in an autonomous X-Y coordinate positioner, which then ensures that the precise holes are cut when the robot is stopped at the appropriate position (right picture).
Remote cutting
Recently, thanks to the increasing power of lasers and the improvement of optical systems (dynamic expander), remote cutting is becoming more and more common in industry. This is mainly for non-metallic materials such as textiles, paper, plastics. In this technology, a two-axis scanning head is placed high on the workpiece at a distance of 1 to 2m. A dynamic expander is placed in front of this scanning head to ensure optimum adjustment of the cutting point size. The beam is deflected across the cutting surface by the two scanning heads in the scanning head, which itself remains in one place during the cutting process.
In laser welding, this method is much more widely used. More details on the principle itself in the next part of the series, which deals with laser welding.
The principle of laser cutting
There are basically three different processes involved in the actual laser cutting process:
- sublimation cutting
- fusion cutting
- flame cutting
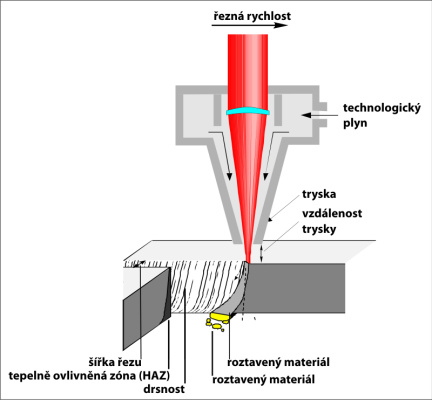
In most cases, laser cutting involves a combination of some of these three processes. The figure below shows the principle of laser cutting.
Sublimation cutting
In sublimation cutting, the material is vaporized from the cutting site. This requires high intensity laser radiation, which is achieved by adjusting the laser parameters and focusing optics appropriately so that the material is instantaneously vaporized. The metal vapour produced is blown out of the cut by the assisting (process) gas. Mostly nitrogen or argon is used as an assist gas to avoid oxidation of the material. Since there is almost no melting of the material, the cut is high quality, smooth and burr-free.
Fusion cutting
Fusion cutting requires lower throughput than sublimation cutting because only the material is melted and the material is blown out of the cutting joint by a stream of inert process gas.
Flame cutting
Flame cutting is used in the cutting of conventional and structural steels because of its high cutting speed. Instead of inert gas, oxygen is used as an assisting gas. The material is heated to a temperature higher than the ignition temperature thus causing an exothermic reaction that energizes the cutting process. Compared to sublimation and fusion cutting, cutting speeds are roughly twice as fast. The quality of the cut is not as good, but is amply sufficient for the vast majority of applications.
Latest trends -
fibre lasers
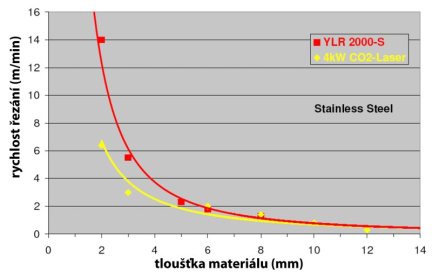
As mentioned above, many CO 2 lasers have been replaced by fiber lasers in recent years. For comparison, the figure below shows a comparison of cutting speeds when cutting stainless steel. As can be seen from the figure, for thinner materials the cutting speed of fiber lasers is significantly higher, even with half the laser power.
In conclusion, the field and issues of laser cutting are quite extensive and countless texts have been written about it. We believe that the information provided in such a limited space will, at least in part, provide interesting information.