Basic overview of industrial lasers
There are five main types of lasers used in current industrial applications, which are listed in the table below. The different types are further subdivided according to the type of excitation, the operating mode (continuous, pulsed) and other parameters. Each type has its own advantages/disadvantages and typical applications for which it is suitable.
The table gives a very basic overview of the individual laser types and therefore the individual parameters listed should be taken with some reserve.
Laser | Wavelength (nm) | Excitation | Effec. a | Mode b | Power / Energy | Typical applications c | Maintenance | Life. (h) |
---|---|---|---|---|---|---|---|---|
Nd:YAG | 1064 | LD | ~7% | CW | up to 6kW | R,S | yes | ~10 000 |
pulsed* | ~ mJ@ns (~100W) | Z,G | ||||||
lamps | ~3% | pulsed* | ~J@ms (~600W) | S,V | ~1000 | |||
CO 2 | 10 600 | RF | ~10% | CW / pulsed | 10-250W | Z,G, Ř nk. | Yes | ~20 000 |
up to 5kW (Slab) | R,S | |||||||
El. | ~25% | up to 20kW (flow-through) | R,S | -- | ||||
Disk | 1070 | LD | ~15% | CW | up to 16 kW | R,S | yes | ~10 000 |
Fibre | 1070 | LD | ~30% | CW | up to 80 kW | R,S | No | ~100 000 |
QCW | ~J@ms (~1.2kW) | Z,G,M | ||||||
Pulsed | ~ mJ@ns (~100W) | Z,G,M | ||||||
Diode | 808-980 | El. | ~60% | CW | up to 10kW | S,K,N | No | ~15 000 |
Basic overview of industrial lasers.
a Efficiency (effectiveness) of conversion of electrical energy into light (optical) energy
b For pulsed lasers, the pulse energy and pulse duration or mean power (in brackets) are given. CW - continuous, QCW - quasi-continuous.
c R - cutting, S - welding, Z - marking, G - engraving, K - hardening, N - coating, M - micro-machining, nk - non-metallic.
Excitation: LD - laser diodes, RF - radio frequency, El. - electric (discharge, current).
Nd:YAG, fiber and disk laser
These 3 types of lasers have a wavelength of ~1µm and belong to the class of solid state lasers - the active medium is a matrix of artificial YAG crystal ( yttrium aluminium garnet ) doped with neodymium (Nd) or ytterbium (Yb) ions. The main difference between these types of lasers is in the geometry of the active medium (figure below) - in Nd:YAG laser the active medium is a rod (length 15-20cm, diameter ~mm), in disk laser it is a thin disk (diameter 10mm, thickness 0,25mm) and in fibre laser it is a long optical fibre (length ~m, diameter 50-300µm).
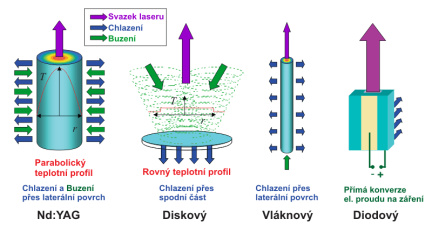
A huge advantage of these three types of lasers is the possibility to conduct their radiation with a wavelength of about 1µm through a flexible optical fiber, which greatly facilitates the "transfer" of radiation from the laser to the process (machining) site.
Nd: YAG laser
Of these types, this is historically the oldest type deployed in industry. The Nd:YAG lasers used are either lamp pumped solid state(LPSS) or diode pumped solid state (DPSS) lasers.
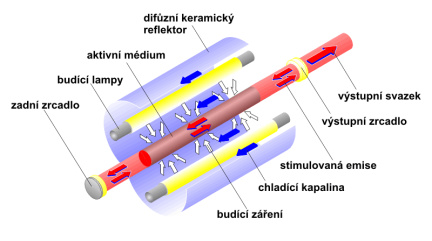
LPSS Nd:YAG lasers have a low conversion efficiency of electrical energy to light energy, as much of the energy of the lamp is not used and is converted to heat (water cooling is required). DPSS Nd:YAG lasers have higher efficiency and better beam quality.
Nowadays, LPSS Nd:YAG lasers are mainly used in pulsed mode for laser welding (applications requiring deep penetration and small temperature-affected zones) and drilling (e.g. in the aerospace industry for drilling stainless steels and alloys). The advantage of these lasers is the high pulse energy (up to 100J@ms) that these applications require. The disadvantages are low efficiency, high cooling requirements, high operating costs and short discharge lifetime (~1000h). IPG Photonics has recently launched an alternative in the form of a so-called quasi-continuous fiber laser (QCW, see table above), which offers identical parameters and at the same time many of the advantages associated with the fiber laser concept.
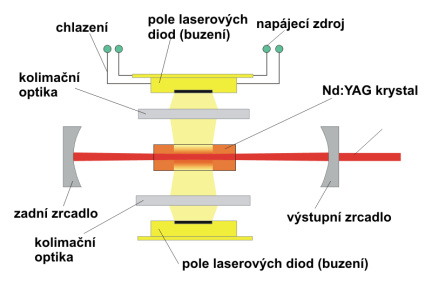
In the case of DPSS Nd:YAG lasers, two main types of excitation are distinguished according to the resonator arrangement - lateral (transverse) excitation and rear excitation (so-called end-pumped ). In rear excitation, the excitation radiation from the laser diodes is guided into the YAG crystal by an optical fiber (note that this is not a fiber laser, which is a common misconception) - the diodes can thus be externally outside the resonator, which is advantageous. If we compare side and rear excitation, then with rear excitation we get better beam quality but lower powers, with side excitation we can get higher powers but the beam quality is lower.
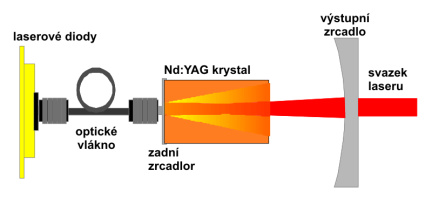
DPSS Nd:YAG lasers are mainly used in the so-called Q-switched pulsed mode, where the laser generates very short pulses in the ns range and the average power is up to 100W. The main application is for marking and engraving of metals, plastics and other materials. Compared to LPSS lasers there is higher efficiency, longer lifetime and less cooling requirements. However, the use of these lasers has been declining strongly for several years and they are being replaced by fiber pulsed lasers, which offer essentially only advantages.
Disk laser
The principle is similar to that of the Nd:YAG laser, but here the active medium is a small disk. The advantage is the flat temperature profile across the disk (picture above), which allows high powers (up to 16kW) with good output beam quality, which was just a big problem with Nd:YAG lasers.
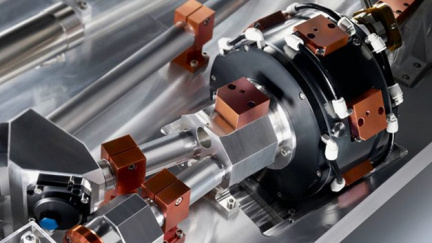
The application is mainly for power intensive operations such as welding and metal cutting. The disadvantages of disk lasers are lower efficiency (15-20%) and lower lifetime than fiber lasers.
Fiber laser
The fibre laser is the most technologically advanced type of solid-state laser, the active medium being a long optical fibre doped with ytterbium (see below). The excitation from the laser diodes is conducted through an optical coupler to the active fibre and instead of mirrors there are Braga gratings, which are structures formed directly on the optical fibre. The radiation is then "pulled" out of the fiber by an optical collimator.
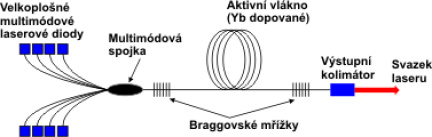
Fibre lasers are further divided according to their operating mode into continuous wave (CW), pulsed or quasi-pulsed (QCW), the main applications of these types can be found in the table above. The great advantage of the fiber laser is its simplicity (the whole laser is actually an optical fiber), robustness and modularity, which is unique to these lasers - the laser is made up of so-called laser modules, the power of which can be gradually increased by connecting them (today up to 80kW).
Other advantages are high efficiency (30-35%), huge lifetime (up to 100 000h), low space requirements, high quality of the laser beam, the lowest operating costs of all the types mentioned and almost zero maintenance requirements.
CO2 lasers
CO2 lasers belong to the group of gas lasers (the active medium is a mixture of gases containingCO2). In industry, lasers are used either radio-frequency (RF) or direct current (DC) lasers. In terms of resonator enclosure, they are divided into sealed off lasers with a hermetically sealed resonator and flow lasers, where the gas flows continuously through the resonator (which is necessary for high power ~10kW).
Up to 5kW, DC RF CO 2 lasers are most commonly used (diffusion cooled, RF excited, basic principle on the right). The excitation of the active gas is performed by radio-frequency waves which pass between two electrodes which, due to their large surface area, simultaneously provide diffusion cooling of the gas in the resonator. These lasers are distinguished by their high reliability, long lifetime and low operating costs.
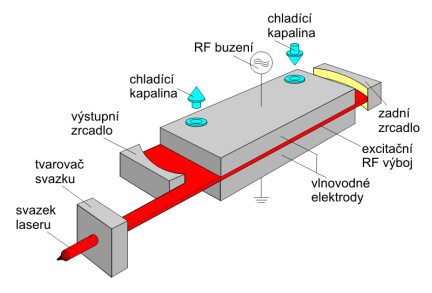
The use of CO 2 lasers is for marking, engraving and cutting of non-metals (plastics, plexiglass, leather, paper, glass, etc.) where the above mentioned 1µm wavelength lasers cannot be used. Here, powers up to 1.5kW are used. Another industrial application is metal cutting and welding (powers up to 20kW) where CO 2 lasers are well established.
Unlike lasers with a wavelength of about 1µm, the CO 2 laser radiation (10.6µm) cannot be guided by optical fibre and mirrors must be used to guide the beam, which is a major disadvantage - the optical path is more complex, regular calibration is required, there are demands on the cleanliness and maintenance of mirrors, etc.
Among the world's major manufacturers of CO 2 lasers is the company Coherent.